With the continuous advancement of technology in the corrugated packaging industry, more and more customers have put forward higher requirements for the printing effect of corrugated boxes, from the simple one-color, two-color, three-color to the four widely used. Color, five-color and other overprinting color, and then to the current six-color, seven-color, even eight-color high-definition ink color printing technology. In response to the increase in the number of these printing color groups, in addition to beautifying the appearance of the carton packaging, it also actively promoted the development of the industry's ink color printing technology.
Although multi-color ink color printing is an environmentally-friendly color printing method, it replaces many offset printing products, which is a promising development prospect. However, through the author's understanding of the industry, there are fewer companies that actually apply this technology. Many business owners have bought back multi-color high-definition watermarkers, but most of them have not played the real effect of the device, and even have Some companies are directly used in the printing of common layouts, which undoubtedly greatly discounts the performance of the device and creates a waste of assets. In response to these problems, the author has accumulated experience in multi-color high-definition watermarking technology management for many years, and now shares several techniques of this technology as the discussion and exchange.
Familiar with device configuration parameters
When buying HD watermarking equipment, the person in charge of the company must understand the positioning of its product packaging and printing. It is necessary to configure the high-definition watermarking machine according to the characteristics of its own packaging and printing, such as the line number configuration of the anilox roller, the number of units of the scraper and the rubber roller, the printing or the printing, etc., and whether or not the slot is provided. Die cutting unit, etc.
The line number configuration of the anilox roller must consider "field layout", "small text line layout", "spot color layout", and "CMYK four-color graphic layout", etc., please refer to the following table for configuration:
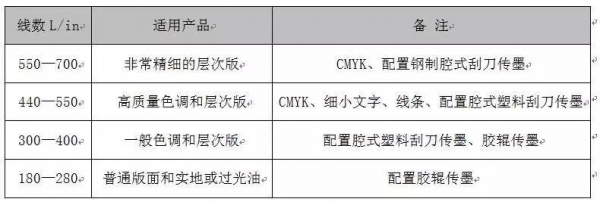
There are pros and cons to choose whether to print or print. The upper printing refers to the printing paperboard from the printing machine. The printing surface is uploaded onto the stacking rack, which can avoid the problem that the printing surface falls on the stacking rack. The lower printing refers to the printing cardboard coming out of the printing press, and the printing surface is dropped down to the stacking rack, which is easy to bring the dirty surface of the printing surface, especially when the winter temperature is low and the ink drying is slow. The problem is more visible. Although the drying device is installed on the high-definition watermarker, it cannot be completely avoided in the state of high-speed printing. To this end, the author suggests that it is appropriate to choose the upper print.
For the need to configure the grooving and die-cutting unit, I recommend adding a set of “drying unitâ€, which is to avoid the squeezing of the squeezing or die-cutting group directly under the condition that the printing surface is not dry yet. Increase printing loss.
Maintain the anilox roller
The anilox roll is the core component of an aqueous printing press and is expensive. The quality and effect of the print have a direct relationship with the anilox roll. To this end, we must pay attention to the protection and maintenance of the anilox roller.
01 After printing, use clean water to clean
The reason why it is required to clean the equipment with clean water is that there are too many groundwater impurities in the area, and many manufacturers have failed to attach importance to installing filtration equipment. These materials with impurities are used to clean the equipment and will be reticulated. The roller causes fatal damage, as shown in the figure, with an anilox roller. Once such an scratch occurs in the anilox roll, the same scratches appear on the surface of the paperboard during printing, which may affect the printing effect or even the defective product.
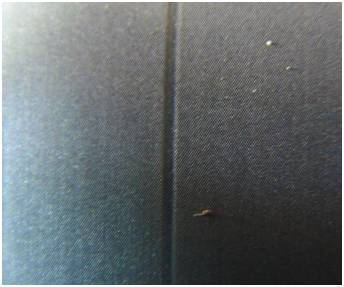
Therefore, the author suggests that there are water-based printing presses and high-end manufacturers, it is necessary to install water filtration devices at the water inlet of the printing press, especially the equipment of the cavity scraper configuration.
02 use clean ink
After the ink is used on the machine several times and then on the machine, or improperly stored, it will often retain some impurity particles. If it is not filtered before the machine, it will cause the anilox roller to be the same as the above-mentioned water cleaning equipment containing impurities. Wear and tear. A good practice is that the ink is preferably filtered with an 80-mesh filter before printing on the machine, so that the anilox roller can be effectively protected.
03 use a clean wipe cloth
When I visited a lot of carton packaging companies, I met a very common phenomenon, that is, the captains and the operators of many printing machines, throwing out the rubbing used for wiping, and throwing them from the ground when they are used up. When you have a hand, you don't have to use a special storage cloth to store the cloth, and even more, the cloth is also used to wipe the device. These are some very bad habits. What's more important is that these bad habits will cause the rubbing cloth to stick the sand on the ground. When rubbing the paper, the sand will often be brought into the layout. After the equipment is in operation, it will be brought into the cavity scraper. If it cannot be eliminated, this is also a detail that will cause scratch damage to the anilox roller. Therefore, it is very important to develop good work habits.
04 anilox roller cleaning regularly
The structure of the anilox roll is composed of a number of regular hexagonal prism-shaped cells. The color change cleaning or post-class cleaning work is not completely cleaned for the anilox roller, especially at the bottom of the cell. The captain can't do regular cleaning. After a long time, the residual ink at the bottom of the cell will accumulate thicker and have a direct influence on the amount of ink transferred by the anilox roller, which will affect the printing effect, resulting in uneven printing color, chromatic aberration, etc. Printing problems. Therefore, the cleaning and maintenance of the anilox roller must be cleaned once a week with a special anilox roller cleaning agent and, if necessary, with a steel brush.
05 cavity scraper that can't be ignored
The cavity scraper cooperates with the anilox roller to play a quantitative and uniform ink transfer function in the water-based printing machine. Its maintenance is good and bad, and it also directly affects the printing effect and the service life of the anilox roller. Therefore, when cleaning the equipment at the end of the printing work, you can't just rely on the automatic cleaning function. You must also open the cavity scraper to check if the inside has been cleaned. If necessary, wipe the scraper with a rag. In addition, it is necessary to check whether the “sponge end seal†at both ends of the scraper chamber is worn out, and if it is worn out, it will be replaced in time to prevent ink leakage during printing.
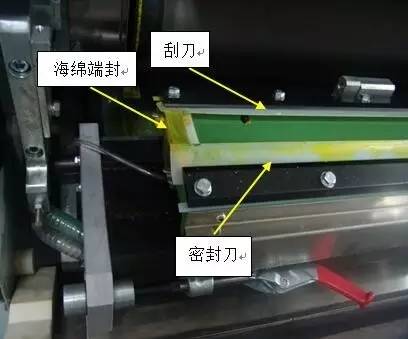
The importance of pre-press review
Since many color overprints or stacked layouts were previously done by offset printing, with the development of multi-color ink color printing technology and the advantages of environmental protection, many previous printings using offset printing are now using more and more colors. HD watermarking technology to complete. But this is not to use the high-definition watermark directly to the offset printing process. This requires full review and design before printing, otherwise it will bring a lot of trouble to the printing process.
01 Pay attention to the overprinting accuracy of the original and the color registration accuracy of the device itself.
As we all know, the offset printing process is a mature printing process, and its color registration accuracy, high printing color reproduction, full color, etc. are its advantages; and the best color-matching equipment in HD watermarking can be achieved. 0.2mm color registration error, plus the flatness of printed cardboard. If you do not do the layout processing on the prepress design, it will cause loopholes in the actual printing process, especially the printed characters, the eyes will run a little bit, and the ghosts will appear. Therefore, it is important to pay attention to this detail when reviewing and prepressing the layout.
02 Note the proportion of the original overlapping dots
The printing process of the multi-color high-definition watermark is a process in which the ink is wet and wet, that is, the ink of the first color is printed under the second color after insufficient drying. If the density ratio of the four-color overlay dots of the original is too high (more than 75%), it is easy to cause poor overprinting problems caused by poor drying of the ink. In order to avoid such problems during the printing process, it is best to notice this when designing the prepress.
In addition to the above problem of poor overprinting, it also causes a problem of printing ghosting. Because the color arrangement of multi-color high-definition watermarks is mainly black-blue-red-yellow, and they are all printed with coated paper. If the front dark ink is too fast to dry sufficiently due to the high proportion of dots, It is easy to bring dark ink to the back of the light-colored ink plate by the paperboard, which causes ghosting print quality problems.
As shown in the figure, it is necessary to know the proportion of the graphic dot on the original plate before printing (a 40-fold microscope can be used or communicate directly with the original designer).
Whether the original is an electronic file is directly related to the printing effect and printing accuracy after the plate making. Due to the fierce competition in the market, some factory salesmen will take the sample box to directly request the plate proofing. If it is the printing of the ordinary layout, there is no problem in doing so. However, for high-definition watermarking, such a phenomenon will cause the effect of post-pressing and the deviation of the original color tone. One of the main factors is that the flexographic dot used for high-definition watermarking has the feature of being enlarged after printing. Therefore, to print a beautiful effect, it is very important to use an electronic version of the original to make a plate.
Control printing pressure
According to the construction principle of the high-definition watermarker, the printing pressure can be divided into "the pressure of the anilox roller and the scraper", the "pressure of the anilox roller and the printing plate", and the "pressure of the printing plate and the cardboard", which are referred to as " Ink transfer pressure, "ink pressure" and "printing pressure". Among them, the ink transfer pressure affects the printing effect relatively small, while the ink pressure and printing pressure directly affect the printing effect due to the level of the operating machine length.
The inking pressure control is mainly adjusted according to the thickness of the printing plate, the printing layout, the printing speed, and the number of times the printing plate is used. If the pressure is adjusted too much, it will directly cause the ink to be squeezed to the edge of the printing plate to form a printing problem of the heavy side; and if the pressure is adjusted too small, the ink cannot be transferred to the printing plate.
The control of the printing pressure is mainly adjusted according to the thickness of the printing plate, the thickness of the corrugated cardboard, and the like. Since the high-definition watermark substrate is a special feature of corrugated cardboard, the pressure adjustment is too large, and the phenomenon of ribs is directly seen on the printing plate surface. The adjusted printing pressure as shown by the yellow circle is as shown:
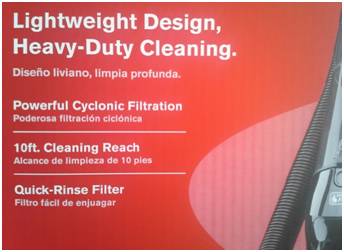
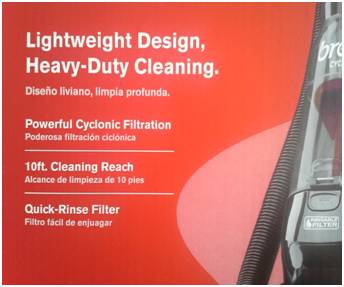
Don't ignore the effects of ink viscosity and pH
In the actual printing process, due to the evaporation of the ink solvent, the viscosity of the ink will gradually increase during use. If it is not controlled, the ink with too high viscosity will bring “paste†and “plug net†to the printed graphic. Quality issues such as "color difference". Therefore, as the main operator of the printing press, it is necessary to observe the ink once every half an hour to ensure the fluidity and stability of the ink.
The pH of aqueous inks is generally between 8.2 and 9.5, and its printability is best. When the pH is higher than 9.5, the alkalinity is too strong, the viscosity of the aqueous ink is lowered, the drying speed is slow, and the water resistance is deteriorated; when the pH is lower than 8.2, the alkalinity is too weak, the viscosity of the aqueous ink is increased, and drying is performed. The speed becomes faster, and the ink is easily dried in the cells of the printing plate and the anilox roller, causing the amount of ink stored in the anilox roller to decrease, and easily causing problems such as dirty plates. Adjusting the PH value of the ink, the ink manufacturer has a PH stabilizer. During the printing process, it is best to be placed next to the machine for easy use.
When, in addition to the above five points of technology, the HD watermarking technology also involves many aspects of technology, such as printing plate, cardboard, ink blending, machine operation, printing process management, etc., all of which are closely related, which requires HD The careful learning of watermark practitioners and enterprise technology managers.
Article source address: http://
Frozen Meat Breaker And Grinder
Frozen meat breaker/frozen meat breaker/meat grinder/meat mincer is the first step of high quality products production. They are used for pre-breaking frozen meat blocks stacked on pallets. It includes bone saw series, frozen meat cutting machine, frozen meat flaker,grinder series, etc. Customers will use different machines depending on the processing needs and to form an automatic production line. No need of defrosting of the meat, Helper`s breaker series has been designed to cut off a whole block of meat in meat pieces with a blades system, avoiding second time pollution and keeping meat texture.
Large frozen meat breaker series: Bone saw, Frozen meat cutting machine, frozen meat flaker.
Frozen meat grinder series: JR-120, JR-140, JR-300, chopping and grinding combination system.
Rib Chopping Machine,Frozen Meat Flaker,Frozen Meat Cutter,Meat Mincer,Meat Grinder,Frozen Meat Breaker
Helper Machinery Group Co., Ltd. , https://www.helperfoodmachiney.com